
They can be used to drill metal, hardwood, and most other materials at greater cutting speeds than carbon steel bits, and have largely High speed steel (HSS) is a form of tool steel high speed steel bits are hard, and much more resistant to heat than high carbon steel. High speed steel taps, feed and speed for both drills and taps and calculator, drill bit terminology and information on our growing company. Since 1951, Norseman™ Drill and Tool - presents our current tools in the product catalog in downloadable sections, along with troubleshooting of high speed steel drill bits and Excessive length increases the chances of complications and poor results.America´s Finest High–Speed Cutting Tools™ You always want to use the shortest boring tool to achieve the cut. For example, you should be able to run at the recommended speed and feed for an insert and material when the nose radius is 0.8mm (0.032”) and the length-to-diameter ratio is 4 to 1 or less. The length-to-diameter ratio of the boring tool and the insert’s nose radius are the two biggest factors in determining the perfect speed. The benefit of slower cutting speed is that it can reduce or eliminate chatter. The surface finish may be worse, the cycle time is longer, and premature insert wear is possible. Lower speed is typically just the opposite. Higher speed also increases the possibility of chatter. Higher speeds will produce a better surface finish, evacuate chips better, and shorten the cycle time. Always follow the speed and feed recommendations for the insert and workpiece material.Īgain, follow the speed recommendations from the speed and feed chart for the insert. If you get chatter in the cut, try increasing the feed per revolution. Don’t worry about finding the size of the honed edge on your inserts. Increasing the feed per revolution will enhance the effectiveness of the chip breaker on the insert and produce a more stable cut. A feed per revolution that is lower than the width of that honed edge can cause deflection and chatter in the cut. Inserts are designed with a honed edge on the tip. If your machine is equipped with a through spindle coolant option, use it! All Haas boring heads are equipped with holes for through-tool coolant. If there is no place for the chips to evacuate the bore, it is extremely important that the chips are broken and flushed out of the bore. In such cases, it is beneficial to use a rough boring head to produce bored holes that are spot-on location and leave a consistent amount of stock for the fine or finish boring head to produce high-tolerance bores with very accurate location, near-perfect roundness, and excellent surface finish.Ĭhip control is key in rough boring applications, especially when boring blind holes. Symmetrical adjustment of the two cartridges produces the best concentricity.ĭrilled holes or holes produced by other means such as end milling may lack the precise location required of tight tolerance holes. They should be adjusted to the same diameter, producing a “two-flute” boring tool. Each cartridge can be individually adjusted. They use two cartridges that each hold a carbide insert.
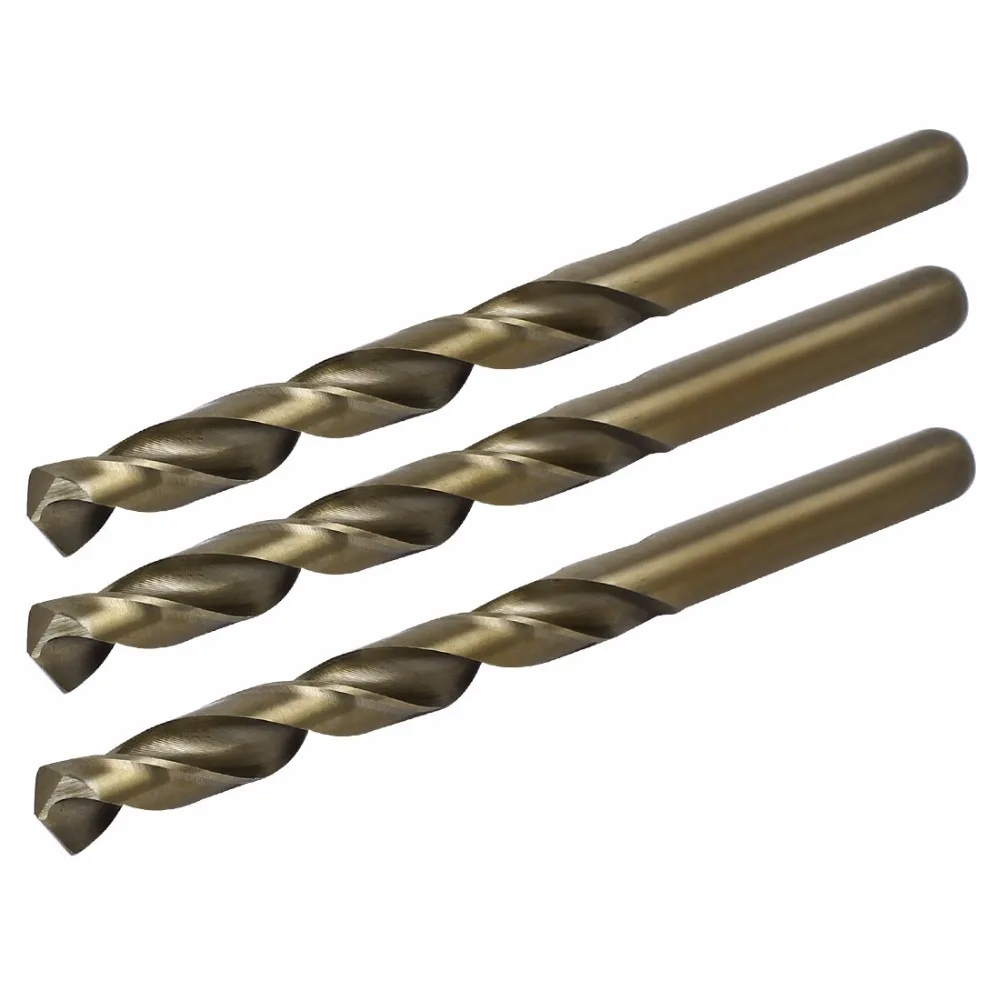
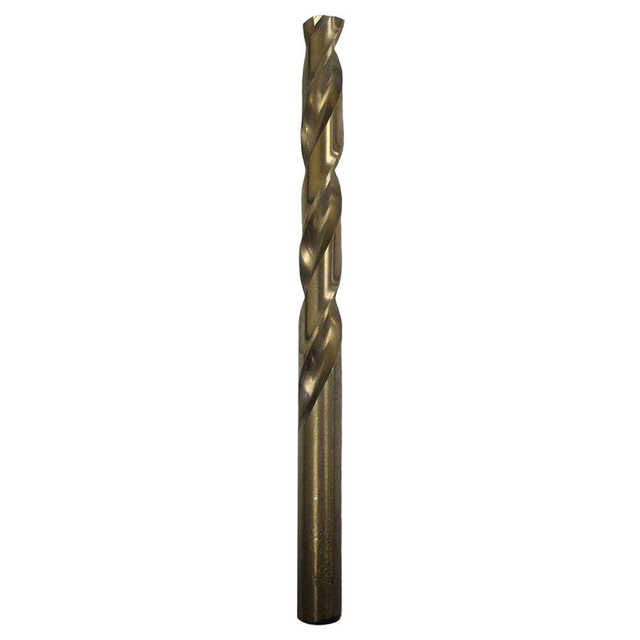
The heads come in 5 sizes but they all share the same characteristics. They are capable of removing up to 10% of the final bore diameter. Rough Bore heads have a twin-bore configuration and are used for rough boring holes.
